Chemical Process Pumps
Chemical processing pumps are critical to the chemical conversion process of manufacturing a finished product. Roth process pumps provide high reliability pumps that are widely known for low life cycle cost and durability under extreme conditions.
Low NPSH Chemical Pumps

Regenerative Turbine Chemical Pumps
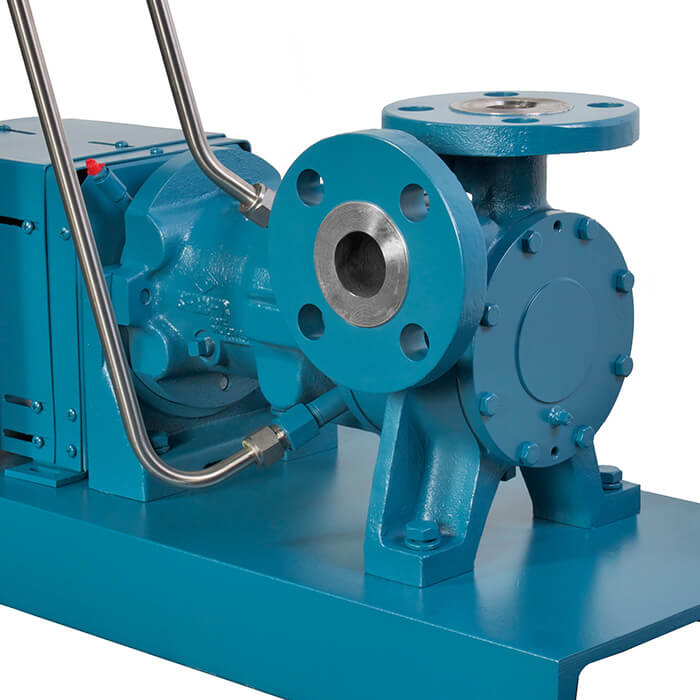
Magdrive Chemical Pumps
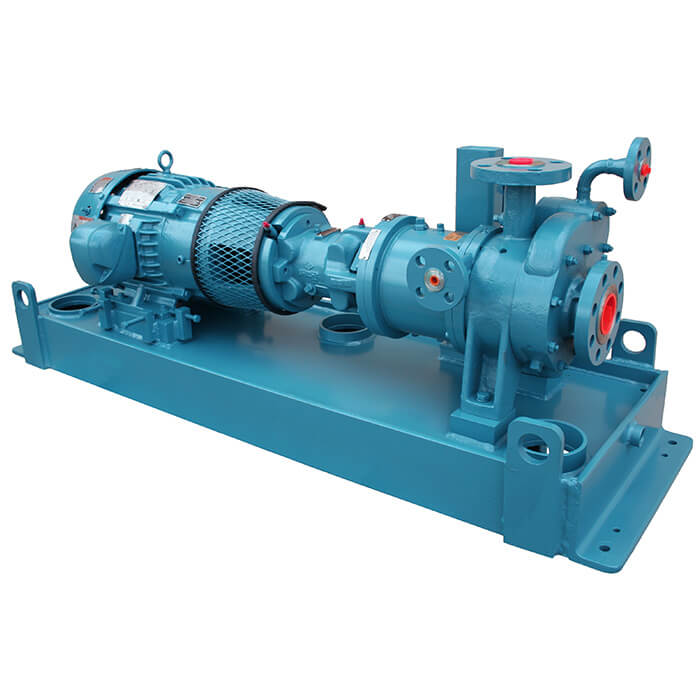
Multistage Low NPSH Chemical Pumps
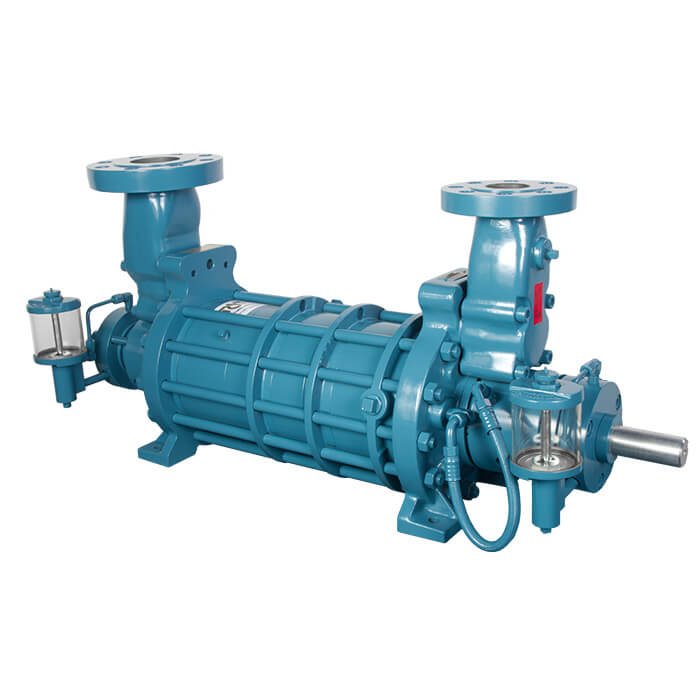
Roth Chemical Processing Pumps
Chemical processing pumps are critical to the chemical conversion process of manufacturing a finished product. Roth process pumps provide high reliability pumps that are widely known for low life cycle cost and durability under extreme conditions. Roth chemical process pumps are widely used in the chemical process, petroleum, and petrochemical industries for low flow high head applications. Roth Pump Company manufactures a variety of chemical processing pumps for improving the operation and efficiency of process systems that can reduce overall process costs. All Roth pumps are regenerative turbine pumps, which provide numerous advantages over centrifugal pump designs.
Regenerative Turbine Pump Design Advantages
What is a chemical pump?
Chemical process pumps are essential equipment used in chemical processing plants to transfer various types of fluids and chemicals. These pumps are designed to handle corrosive and hazardous materials, making them a critical component in any chemical processing plant. Chemical process pumps come in different types, such as centrifugal pumps, diaphragm pumps, gear pumps, and positive displacement pumps, each with its unique features and benefits. Regenerative turbine pumps are a type of pump between a centrifugal pump and a positive displacement pump that has a unique impeller design that makes them highly effective for handling low flow and high-pressure applications. These pumps are widely used in the chemical processing industry for a wide range of applications, including the transfer of solvents, chemicals, and acids.
Chemical process pump advantage
One of the primary advantages of regenerative turbine pumps is their ability to generate high pressure even at low flow rates. This is achieved through the impeller's unique design, which uses a series of blades that force fluid to move in a circular path around the impeller. This results in a pressure boost that is continually reinforced as the fluid moves through the impeller, making it an ideal choice for applications that require high pressure, such as the transfer of chemicals into a reactor vessel.
Regenerative turbine pumps are also well-suited for handling viscous fluids, such as solvents and acids. They can handle fluids with viscosities up to 200 centipoise and are capable of transferring fluids at temperatures up to 450˚F. In chemical processing applications, regenerative turbine pumps are often used to transfer chemicals from storage tanks to reactor vessels or to move chemicals into a mixing vessel. They are also used to circulate fluids through heat exchangers or to transfer chemicals between different processing steps.
When selecting a regenerative turbine pump for chemical processing applications, it is essential to consider factors such as the type of fluid being transferred, the required flow rate, and the operating conditions. It is also crucial to ensure that the pump is made of materials that are compatible with the fluid being transferred to avoid any corrosion or chemical reactions.
Regenerative turbine pumps are an excellent choice for chemical processing applications that require high pressure and low flow rates. The unique impeller design makes them effective for handling viscous fluids, abrasive chemicals, and fluids containing small particles or solids. When selecting a regenerative turbine pump, it is essential to consider factors such as the type of fluid being transferred, the required flow rate, and the operating conditions, to ensure that the pump can perform optimally and provide years of trouble-free operation.
View Liquids Pumps